The Clouth Cleaning Systems in use
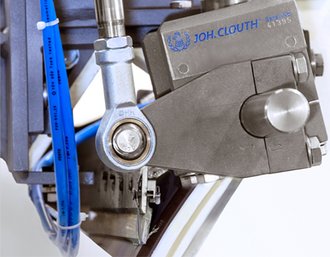
In 2019, Clouth cleaning systems were installed in Automotive Line No. 3 at Speira (formerly Hydro Aluminium Rolled Products GmbH). Read our experience report published at that time about the planning, installation and success of the Clouth products used here.
Clean Processes for more Efficiency, Quality and Safety: Cleaning Systems delivered by the Clouth Group to Speira's (formerly Hydro) New Automotive Line No. 3
Sometimes it’s the small, almost invisible components that have a decisive influence on the efficiency of a production process. This is the case with the doctoring systems delivered by the Clouth Group. They make a substantial contribution to the quality and safety of the new automotive line No. 3 - and this is by ensuring the cleanliness of the rollers.
A Milestone for the Lightweight Automotive Construction
The highly modern automotive line No. 3 in Grevenbroich has been in operation since May 2017. It delivers aluminium parts to the leading automotive manufacturers in Europe who produce lighter vehicles with these parts and reduce the CO2 emissions in their new cars. The most modern aluminum strips are produced in a loop within the 190m long plant which must meet the quality requirements of customers like Mercedes-Benz, Audi, BMW, Peugeot, or Citroën. To ensure this, it is vital to avoid any pressure-marks caused by even the smallest particles which could come occur in the tacking process of the aluminium strips. One possible option here is the installation of doctoring systems, which significantly reduce the deposits on the rollers with no adverse effects on their performance.
The decision to select systems from the Clouth Group – produced from components at the sites in Eltmann and Hückeswagen – was made following the recommendation of the BWG Bergwerk- und Walzwerk-Maschinenbau GmbH, who is the overall plant supplier and responsible for the system. For more than ten years BWG have successfully implemented projects together with Clouth all over the world, because Clouth is an established and trusted supplier and partner, known for providing on-the-spot consultancy and a quick service under pressure.
Doctor Blade and Roller in Harmony
The Clouth cleaning systems have been implemented step-by-step where they have been needed. Detailed documentation of the production from the beginning, allowed exact conclusions as to the corresponding roller positions. The doctor blade used was the CLOUTH-AS® and the holder was a CLOUTHFLEX®-18 VA mini, each of them has been individually adapted to the specific conditions and requirements. The specific requirements for the conditions and electrical engineering could be set-up individually, meaning that there was no need for the plant to be shut during the trial run. Clouth systems excellently fit into the maintenance cycle of the plant, thus no separate maintenance interval needs to be planned here.
Effectively Working Right from the Beginning
Already with the installation of the first four Clouth systems, significant improvements regarding the material and surface quality of the coils could be achieved. Lutz Kaufmann, being involved as project engineer from the planning to the start-up of the progressive automotive line No. 3, remembers: <<It was immediately clear that with the Clouth doctoring systems we are on the right track. This made it easy to decide to install additional systems from Clouth>>.
Meanwhile there are in total 15 doctoring systems in use over the entire automotive line No. 3. At the roller positions where these systems have been installed, the error rate could be reduced by 90 %. And the efforts with regards to tool deficiencies could be decreased by about 1.5 hours per week. The minimized contamination of the surfaces makes longer, undisturbed production cycles possible. Moreover, the Clouth systems excellently fit into the maintenance cycle of the plant, thus no separate maintenance interval needs to be planned here.
Teamwork at Eye Level
Regarding to the co-operation with Clouth technicians, Lutz Kaufmann expressed his enthusiasm: ‘The installation on the part of Clouth was done in a quick and easy way by their own team of experienced installers which perfectly attuned to the plant and our processes.’
So, excellent conditions for continue cooperation are in place: At the moment, as a retrofitting measure, an installation of doctoring systems in the two other Speira (formerly Hydro) automotive lines. Nos. 1 and 2 has been agreed.
Marcus Herziger, Sales Manager Non-Paper at Joh. Clouth in Hückeswagen, adds: ‘Herein, the proven Clouth modular construction system comes in useful. Products which have been installed within the new automotive line No. 3 as well can be adapted to already existing plant concepts.’
Another use of Clouth doctoring systems is planned for the product range ‘lithography’ – of course, customized for the given plant and production environment.
Photo: Lutz Kaufmann (on the left), responsible Project Eng. at that time at Speira (formerly Hydro), and Marcus Herziger (on the right), Sales Mgr Non-Paper at Clouth in Discussion on the Clouth Cleaning Systems at the Automotive Line No. 3